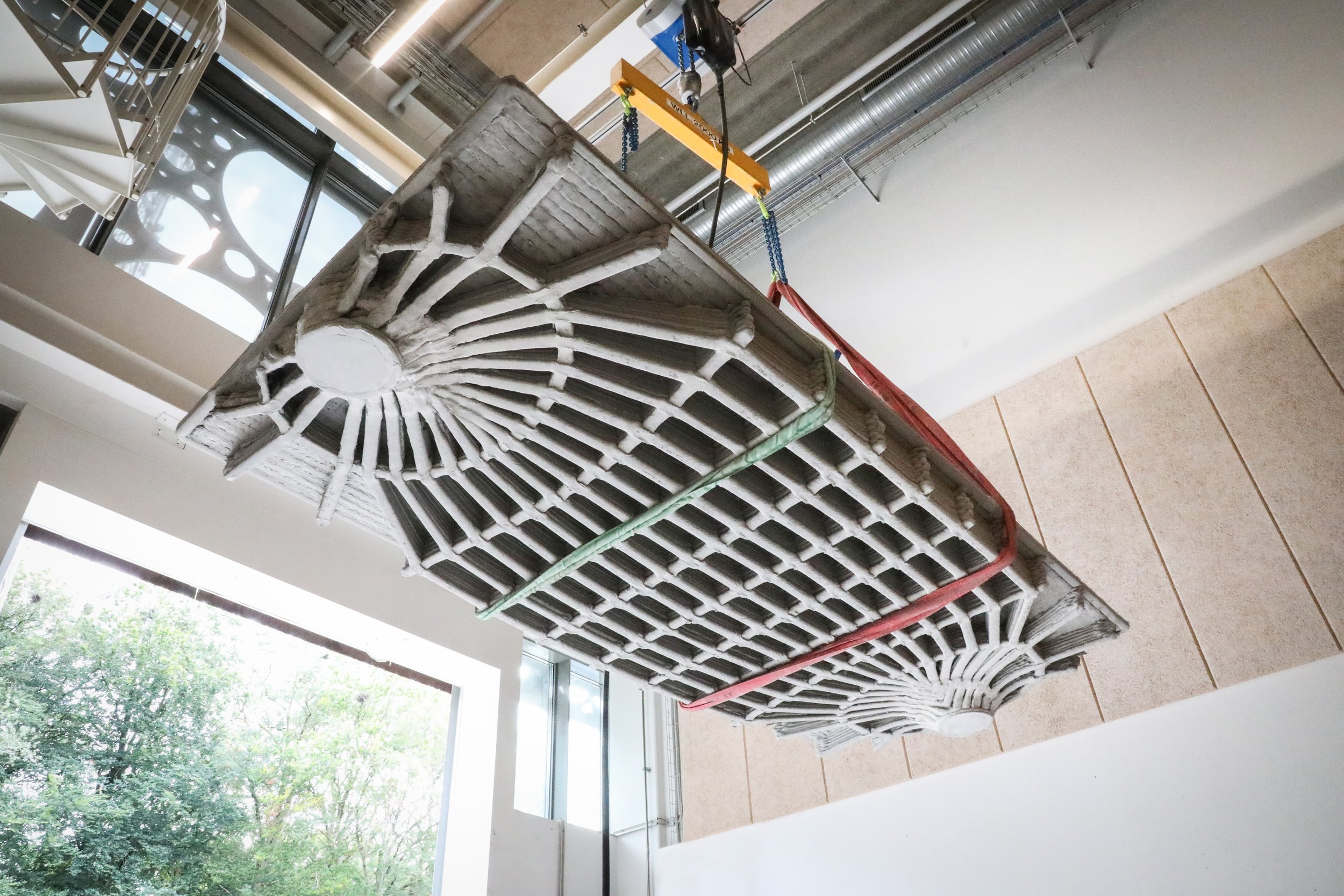
3D printed concrete slabs can make construction greener
SDU CREATE at the Faculty of Engineering has developed a 3D-printed concrete slab that requires significantly fewer materials than traditional slabs and thereby also emits less CO2.
Load-bearing concrete slabs make up around 40-45% of the total concrete consumption in mid-rise buildings. And since as much as 8% of global CO2 emissions come from concrete production, there is good reason to take a closer look at the horizontal surfaces we walk on and find out if they can be made smarter.
And they can, according to Roberto Naboni. He is an associate professor at the Department of Technology and Innovation at SDU and leader of the research center SDU CREATE.
Together with PhD student Luca Breseghello and other colleagues from SDU CREATE, Roberto Naboni has developed a new 3D-printed concrete slab in the research project 3DLightSlab. The study has been published in Journal of Building Engineering.
The advantage of 3D-printing the structure is that the computer can calculate the most optimal structure for the slab, making it significantly slimmer and tailored to the specific building and the required strength at that specific site. This way, materials are saved, thereby also reducing greenhouse gas emissions and resource consumption.
- This project explores using the flexibility of 3D concrete printing to reduce CO2 emissions of such structural elements.We have introduced a computational method that allows the automated design of slabs optimised for specific loads and geometries of any building, explains Roberto Naboni.
Exactly how much concrete and CO2 emissions that can be saved compared to traditional concrete slabs will vary from case to case, and it is still to early to present accurate numbers.
- Our primary achievement has been demonstrating the feasibility and practical application of this technology. The key advantages lie in the potential reduction of embodied carbon, waste, and workforce requirements, alongside offering maximum design flexibility—an aspect that is traditionally very costly but made more accessible by our technology.
Inspired by nature
The 3D-printed concrete slab is, in several ways, a breakthrough.
- Up to now, there was no established knowledge on how to 3D print load-bearing horizontal structures of this kind. Our approach involves embedding steel reinforcements within 3D printed filaments, which had not been done at this scale before, says Roberto Naboni.
One of the sources of inspiration for the research group has been how nature creates structures, explains the researcher.
If you think about the human body, a tree, or a spider's web, its structure is also designed to be as light as possible while still being attuned to the loads it must withstand.
- In our design, we focus on principal stresses, which are flows of pure tension and compression within structures. Nature builds lightweight, strong structures, such as human bones, according to these stresses, says Roberto Naboni.
Advanced computational models
But where nature has had millions of years to refine its constructions through evolution, the researchers at SDU have had to use computer models and simulations to figure out how the slabs should be made.
- Predicting the structural behaviour of these slabs poses a significant challenge. This required detailed modelling of the printing sequence, material allocation, and the fabrication process, involving the combined use of finite element simulations, says the associate professor.
In the 3DLightSlab project, Roberto Naboni and his colleagues have continuously tested and validated the slabs in collaboration with SDU Structures, and they meet the standards within the construction industry.
He, therefore, expects that the technology will soon find its way to the real construction sites.
- We estimate that this technology could be market-ready within 24 months. Our findings suggest that, despite being a new technology, it holds theoretical potential for economic efficiency and sustainability. The main steps towards market readiness include further engineering for industrialization and partnering with designers and constructors willing to innovate. We are already in contact with some important players in Denmark and Europe. Initial projects will require comprehensive engineering case studies and extensive testing, tasks we are prepared to undertake at SDU CREATE.
Read more at SDU CREATE.