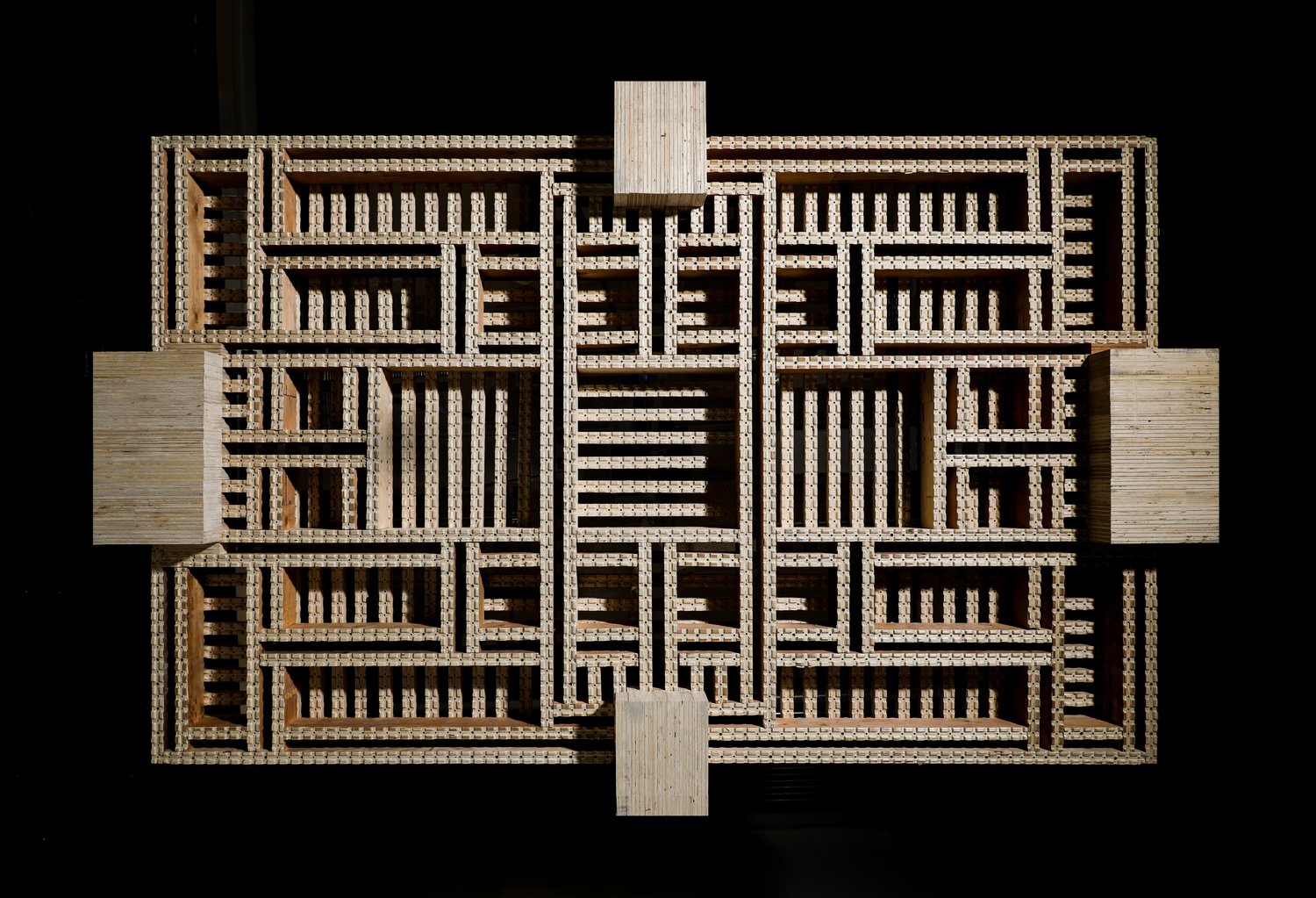
The future of building: Here is the Lego of the construction industry
Researchers at the University of Southern Denmark are working to make the construction industry more sustainable with Lego-like wooden modules that can be assembled into load-bearing structures, disassembled, and reused repeatedly using robots and digital models.
With Lego bricks, you can build almost anything. You can put them together one way and then another, make changes, add more, reuse them again and again, and even pass them on to children and grandchildren who can do the same.
Imagine if you could do the same on a large scale in construction.
Perhaps the scenario is not so far off. At least, creating the construction industry's answer to Lego is the ambition behind the research project ReconWood at the University of Southern Denmark (SDU).
Instead of small plastic bricks, researchers are working with slightly larger wooden modules designed to be easily assembled and disassembled and used to build everything from load-bearing columns, walls, and beams to entire floor slabs.
The idea is that they can be assembled automatically by robots or manually with the aid of VR glasses.
Furthermore, using QR codes and a digital database, one can keep track of the history of each brick, just as one can build and test simulations of the constructions on a computer – also known as digital twins – before starting in reality.
Buildings are a carbon capture technology
The project is led by associate professor Roberto Naboni and PhD student Anja Kunic from the Faculty of Engineering at the University of Southern Denmark. They are part of the research group SDU CREATE, which works to bring new technologies into architecture and construction to make it more sustainable.
And there are many reasons why ReconWood is a good idea, the researchers say.
- Right now, wood is the only 100% sustainable building material, but if we are to build more in wood, it will put pressure on the forests. Also, when wooden structures are demolished, as things stand today, the wood is often incinerated, causing even more CO2 emissions, says Anja Kunic.
- Therefore, it is important to keep the building materials alive for as long as possible, and this can be done if they are modular and reconfigurable
In the construction industry in Denmark, the general lifespan of buildings is estimated at 50 years. Sometimes buildings stand much longer, sometimes shorter, but in any case, it is important to remember that even a brand-new building will eventually need to be rebuilt or demolished because needs have changed.
- It is extremely important that we can then reuse the materials the buildings are made of because they contain a lot of stored CO2. You could almost say that buildings are a kind of carbon capture technology. But the energy that nature has used to create the materials is wasted if you just tear down or rebuild without reusing, explains Roberto Naboni.
Construction of the future
Of course, one can already reuse, for example, wooden beams and rafters today, and this is also being researched at SDU. But there are several challenges associated with it, say the researchers. For example, in larger constructions, it can be difficult to obtain enough used materials of the right dimensions.
These challenges are avoided by, from the very beginning, working with modules designed to be assembled and disassembled repeatedly.
And the ReconWood constructions are just as strong as traditional wooden constructions, the researchers say.
- The modules themselves are milled, completely automated, from LVL – or laminated veneer lumber – and they are assembled without glue, only with screws and bolts in pre-drilled holes, explains Anja Kunic.
- The smart thing is that because it is so flexible, you can easily strengthen the construction in the places in buildings where there is a need for great strength and make it lighter in the places that are not as exposed. In this way, you can use fewer materials. A problem with conventional CLT construction is that you quite often over-dimension.
The project is still in research phase, so we should not expect ReconWood building blocks in hardware stores already next year. But the researchers are currently looking into a possible commercialization, and they are in no doubt that the principles behind the project will be part of the construction of the future.
The people behind ReconWood
SDU CREATE, Led by Ass. Prof. Dr. Roberto Naboni - University of Southern Denmark
Concept and Scientific Development: Anja Kunic, Roberto Naboni
Design and Engineering: Anja Kunic, Davide Angeletti, Giuseppe Marrone, Hamed Hajikarimian, Roberto Naboni
Fabrication and Construction: Anja Kunic, Davide Angeletti, Giuseppe Marrone, Pedro Vindrola, Daniele Florenzano
Robot Planning: Anja Kunic, Ardeshir Talei
Technical Support: Pedro Vindrola (MR UI), Ardeshir Talaei (Data management and databases)
Material
Partners: Stora
Enso
Supported by Industry 4.0 Lab (SDU)