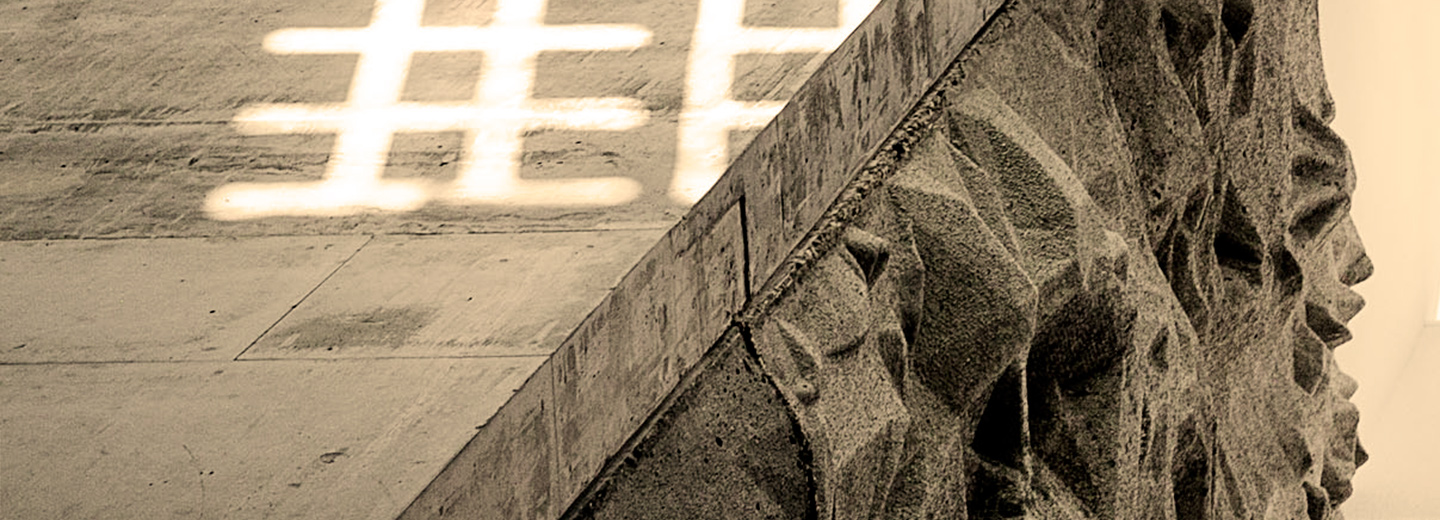
Robots set to make aircraft parts
Although steel has been replaced with modern composite materials in cars, aircraft and wind turbine blades, robots have not yet learned to work with the new materials. But they will now. A consortium led by the University of Southern Denmark has received 13 million kroner from Innovationsfonden to upgrade robots.
The use of steel has long ago been shelved. Cars, aircraft, wind turbine blades and even golf clubs are today produced using advanced composite materials. Industry has replaced steel with modern materials that weigh much less without compromising on strength.
The only problem is that robots haven't yet learned to handle the new materials. But now robots are going back to school to learn how to work with fiber composite materials.
A consortium of Danish and international researchers led by the University of Southern Denmark has received 13 million kroner from Innovationsfonden to develop a completely new type of automation.
- The problem is that is takes an enormous amount of pay cheques to handle fibre composite materials. For instance, when Terma Aerostructures produces aircraft parts it is done manually, explains Professor Henrik Gordon Petersen from SDU Robotics and continues:
- At present, aircraft parts are molded by mats which consist of carbon fibre threads impregnated with adhesive. An employee layers the mats, which are approximately 0.2 mm thick, on top of each other until the desired geometry is achieved without any air bubbles occurring. It is like trying to stick cling film to a vase.
Clear competitive advantage
It is this process which until now has been too much of a challenge for robots. But if researchers succeed in automating work with composite materials, Denmark will have a clear competitive advantage that will extend to all branches of industry that have shelved the use of steel.
- Even for humans, it is a difficult process. A robot has the advantage that it is not limited to two hands and we can equip it with a two dimensional arsenal of suction pads. The suction pads must be able to turn and adapt to any kind of structure the mat is placed on, exlpains Henrik Gordon Petersen.
Fewer flaws
Henrik Gordon Petersen hopes that by developing a method for auotmating the work, the consortium can create the basis for a wide range of new Danish jobs in the production of flawless composite materials.
- It is also our goal that the system will reduce the number of flaws. For example, we need to avoid creases when the mats are laid on the mould. If a flaw does occur, the system will find it with computer vision and where possible the robot system will automatically learn to correct the process so that flaws don't occur again, says Henrik Gordon Petersen.