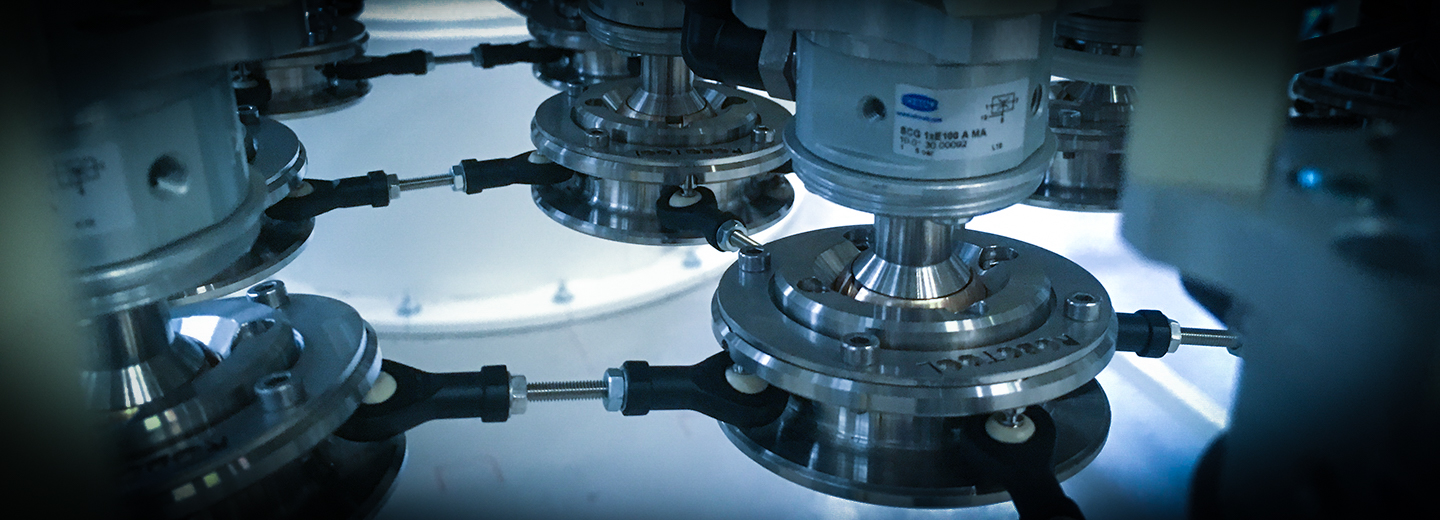
Robots take the lead in composite construction
A robot mounted with 80 suction cups is to build aircraft parts at Terma. With a grant from Innovation Fund Denmark, robot researchers at the University of Southern Denmark are well on the way to automating the production of composite parts, thereby securing Danish companies a great competitive advantage.
Composite materials are popular. Particularly within the aviation, car and wind turbine industries, parts are replaced with the strong and light carbon fibre material. The use of composite materials is growing by 12% each year.
However, the use of composite is not more widespread because it is expensive to produce. Therefore, researchers at SDU are working on finding a robot solution that will make composite parts cheaper.
- At the moment, we're world leaders in the race to develop robot solutions in the production of composite. The use of composite is undergoing rapid development, and if we can make composite much cheaper by automating the production of composite parts it will be a discovery with far-reaching effects, says Professor Henrik Gordon Petersen from SDU Robotics.
Automation creates unique competitive advantages
Henrik Gordon Petersen has just received over DKK 8 million from Innovation Fund Denmark for the project FlexDraperProduct. By 2020, the aim is for the researchers to have come so far in the development of a robot solution for automatic production of fibre mats for composite parts that Terma will invest in the solution.
For three years, researchers have worked closely with Terma on developing robots that can build composite parts.
At present, composite parts are built up of many layers of fibre mats. The mats are made of an adhesive material which is placed on a mould. Layer upon layer. Without creating critical air bubbles or folds under the mats.
”At the moment, we're world leaders in the race to develop robot solutions in the production of composite.
The long complicated process is carried out manually by one person, which makes the composite parts expensive.
- It would considerably improve our competitive edge if we were able to automate the most time-consuming process in the whole production of composite parts - the manual laying of the mats.
The research project
- Name: FlexDraperProduct
- Grant: DKK 8,147,649 from Innovation Fund Denmark
- Budget: DKK 11,769,213
- Partners: SDU, Terma, DTU, Aalborg University, Technicon, NLR
- Automation is also an important link in our digitalisation of production and a groundbreaking example of how we are utilising a digital thread from design and all the way to production in the factory, explains Vice President Jesper Freltoft from Terma.
Jesper Freltoft also points out that Terma's position at the forefront of the international competition to find an automated robot solution in the production of composite parts makes the company from Grenaa attractive to the world's leading aircraft producers.
Suction cups replace hands
The starting point is a developed robot that holds a tool with 80 suction cups that can adjust themselves in relation to each other to achieve the desired shape. The suction cups use a vacuum to carefully hold and position the mat on the mould.
- We've reached a point where our automated system can handle the simplest composite parts, but now we are going to develop and test the system on parts with more curves.
-It's very complicated to get the suction cups to position the fibre mats on moulds with bigger curves without critical air bubbles forming under the mat, explains Henrik Gordon Petersen.
Testing the product on aircraft parts
At Terma, the starting point is to test the technology on their production of aircraft parts for Lockheed Martin's F-35 fighter jets, but the technology will later be used in many other industries in which composite parts are produced - both within and outside of the aviation industry.
- Of course, it's always easiest to get things to work in the laboratory. There will undoubtedly be challenges when we begin testing on a larger scale in a production environment - where the tolerance and patience for mistakes is very limited, says Jesper Freltoft.